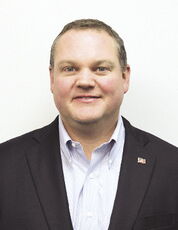
Please do not leave this page until complete. This can take a few moments.
You’re driving down the highway dreaming of the French fries you’ll eat when you pull into the rest area.
Sometimes, the fries are crispy and piping hot. Other times, they’re soggy and cold. Did you ever wonder why?
Some quick-service restaurants, as fast-food establishments are known in the industry, use “smart cooking” computers to cook the perfect bag of fries. The devices know whether the food-service worker has dumped a handful of fries into the fryer or an entire bag.
Then, the controller will tell the worker how long they need to cook and how long they can be held before they’re no longer good for sale.
Kitchen Brains, a 53-year-old company in Stratford, manufactures the process controls and timers embedded in all kinds of commercial cooking appliances, not just the French-fry equipment.
They also produce QPM, which stands for quality production manager, a proprietary software that works with the controls to enable automation and lets the kitchen staff know what items are available to sell and how long they will last, among other data points.
The controls monitor time, temperature and the holding of food. They can alert staff that a freezer door is open, or that a product has been held too long and must be thrown out.
The controls help with food safety, consistency and quality, said CEO Christian Koether.
Kitchen Brains’ equipment automates the entire cooking process so that decisions are already made for staff.
Retooling operations
Kitchen Brains partnered with Microsoft Azure to provide cloud connectivity for the data collected by the smart cooking appliances.
The controls are sold to Kentucky Fried Chicken and other fast-food chains around the world as well as fine-dining restaurants, convenience stores, hospitals and stadiums. Although the manufacturing center is in Stratford, the company has a technology center in Fort Lauderdale, Florida, and offices in London, Shanghai and Singapore.
When the COVID pandemic upended the restaurant industry and demand for controls stopped, Kitchen Brains saw an opportunity to take stock and grow.
“Since we had nothing to do, we thought we might as well go out and buy all new equipment,” Koether said with a laugh. “We spent close to $2 million. We took a risky move and retooled our entire manufacturing department.”
The new equipment will enable Kitchen Brains to increase production capacity by 40 percent. Both retail customers and original equipment manufacturers have expressed an interest in purchasing American-made controllers and that led Kitchen Brains to expand.
The company recently opened an Advanced Technology Center in Florida where all of its Internet of Things and cloud development team will work. In Stratford, they reallocated space formerly used by the software team to house the new manufacturing equipment.
The controls are built on a surface mount technology or SMT line. It is equipment that automates the mounting of electronic components directly onto the surface of printed circuit boards. In July 2020, the company installed two new SMT lines, a wave solder machine, and new optical inspection equipment.
In August 2020, sales ramped up with the reopening of highway rest areas, coming back stronger than before the pandemic.
The company currently employs 110 people. About half work in direct labor. The others are engineers, marketing and sales employees, administrative personnel and leadership. The company declined to disclose its annual revenues.
The goal is to create more jobs, Koether said. The company currently runs 1.5 shifts per day and will add employees to support the new equipment being installed, allowing them to increase production capacity by 40 percent.
Kitchen Brains also received a subsidy from the Connecticut Department of Labor to cover part of the program cost of working with CONNSTEP, a Hartford-based manufacturing consulting firm that is part of the Connecticut Business & Industry Association.
CONNSTEP trained the Kitchen Brains workforce in lean manufacturing and process improvement techniques. Lean teaches companies to cut waste in any form, including any extra labor, time or materials spent creating a service or product that doesn’t add value to the end result.
“We trained everyone on lean in an effort to remain competitive,” Koether said. “Connecticut is not the easiest place to run a manufacturing plant. There’s a lack of talent in Connecticut and there are more tax advantages to build controls elsewhere.”
Despite these challenges, Koether is loyal to Connecticut, he said.
The company was founded in 1969 by his father. Earlier this year, the family decided to partner with Source Capital LLC, a private equity firm that acquired the company.
“We have no intention of relocating,” Koether said. “Hopefully, we will be here another 53 years. We hope to bring more business into this plant. We are here for the long haul.”
This special edition informs and connects businesses with nonprofit organizations that are aligned with what they care about. Each nonprofit profile provides a crisp snapshot of the organization’s mission, goals, area of service, giving and volunteer opportunities and board leadership.
Learn moreHartford Business Journal provides the top coverage of news, trends, data, politics and personalities of the area’s business community. Get the news and information you need from the award-winning writers at HBJ. Don’t miss out - subscribe today.
SubscribeDelivering Vital Marketplace Content and Context to Senior Decision Makers Throughout Greater Hartford and the State ... All Year Long!
Read HereThis special edition informs and connects businesses with nonprofit organizations that are aligned with what they care about. Each nonprofit profile provides a crisp snapshot of the organization’s mission, goals, area of service, giving and volunteer opportunities and board leadership.
Hartford Business Journal provides the top coverage of news, trends, data, politics and personalities of the area’s business community. Get the news and information you need from the award-winning writers at HBJ. Don’t miss out - subscribe today.
Delivering Vital Marketplace Content and Context to Senior Decision Makers Throughout Greater Hartford and the State ... All Year Long!
In order to use this feature, we need some information from you. You can also login or register for a free account.
By clicking submit you are agreeing to our cookie usage and Privacy Policy
Already have an account? Login
Already have an account? Login
Want to create an account? Register
In order to use this feature, we need some information from you. You can also login or register for a free account.
By clicking submit you are agreeing to our cookie usage and Privacy Policy
Already have an account? Login
Already have an account? Login
Want to create an account? Register
This website uses cookies to ensure you get the best experience on our website. Our privacy policy
To ensure the best experience on our website, articles cannot be read without allowing cookies. Please allow cookies to continue reading. Our privacy policy
0 Comments